Smart Manufacturing: The Key to Cutting Costs in Industrial Production
As the world relies increasingly on technology and automation, the manufacturing industry is no exception. Smart manufacturing is a concept that has emerged as a solution to many of the challenges faced by traditional manufacturing methods. In this blog, I will explore the benefits of smart manufacturing, its role in quality control, and how it can help reduce manufacturing costs. I will also provide case studies of successful smart manufacturing implementations and offer tips for overcoming common manufacturing problems.
Introduction to Smart Manufacturing
Smart manufacturing, also known as Industry 4.0 or the Fourth Industrial Revolution, is the use of advanced technologies and data analytics to optimize and automate manufacturing processes. It involves the integration of various technologies such as the Internet of Things (IoT), artificial intelligence (AI), robotics, cloud computing, and big data analytics to create a more efficient and flexible manufacturing system.
Smart manufacturing enables companies to collect, analyze and act on real-time data from their manufacturing processes, machines, and supply chain. This allows them to identify potential problems, reduce waste, optimize production schedules, and improve overall quality and efficiency. By leveraging smart manufacturing technologies, companies can also improve their responsiveness to changing customer needs, reduce lead times, and lower costs.
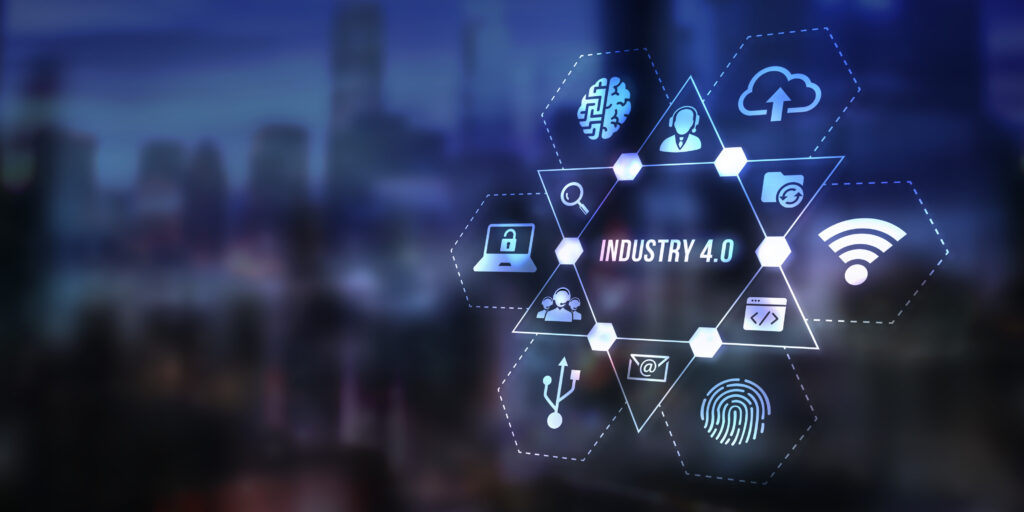
Understanding the Challenges in Traditional Manufacturing
Traditional manufacturing methods are often plagued by inefficiencies, such as long lead times, high scrap rates, and poor quality control. In addition, traditional manufacturing methods are often unable to keep up with the changing demands of customers and the market. These challenges have led to the development of Industry 4.0 in manufacturing.
Traditional manufacturing faces several challenges that can limit efficiency and productivity, including:
Limited visibility: In traditional manufacturing, it can be difficult to get an accurate picture of the entire production process. This can result in delays, quality issues, and inefficiencies.
Lack of flexibility: Traditional manufacturing systems are often rigid and inflexible, making it difficult to respond quickly to changes in demand or product design.
High costs: Traditional manufacturing can be expensive, with high labor and material costs, as well as the costs associated with maintaining and upgrading equipment.
Quality issues: Traditional manufacturing can be prone to errors and quality issues, which can result in waste, rework, and customer dissatisfaction.
Environmental impact: Traditional manufacturing can have a significant environmental impact, with high levels of energy consumption, waste generation, and greenhouse gas emissions.
Limited innovation: Traditional manufacturing can be slow to adopt new technologies and processes, which can limit innovation and competitiveness.
Industry 4.0 in Manufacturing
Industry 4.0 is a term used to describe the fourth industrial revolution, which is characterized by the integration of advanced technologies into the manufacturing process. The goal of Industry 4.0 is to create a more efficient, productive, and flexible manufacturing environment that can respond quickly to changing market demands. Smart manufacturing is a key component of Industry 4.0.
Benefits of Smart Manufacturing
The benefits of smart manufacturing are numerous. It can increase efficiency, reduce lead times, and improve product quality. Smart manufacturing can also help reduce costs by optimizing production processes and reducing waste. In addition, smart manufacturing can help manufacturers respond more quickly to changing market demands, which is critical in today’s fast-paced business environment.
We can divide benefits of Smart Manufacturing into seven categories:
Improved efficiency: Smart manufacturing technologies can optimize and automate manufacturing processes, leading to improved efficiency and productivity.
Increased flexibility: Smart manufacturing can enable manufacturers to quickly adapt to changing market demands, customer needs, and product designs.
Enhanced quality: Smart manufacturing technologies can help manufacturers detect and prevent defects, reduce waste, and improve overall quality.
Greater sustainability: Smart manufacturing can reduce energy consumption, waste generation, and greenhouse gas emissions, leading to a more sustainable manufacturing system.
Improved decision-making: Smart manufacturing technologies can provide real-time data and analytics, enabling manufacturers to make more informed and data-driven decisions.
Cost savings: Smart manufacturing can reduce labor costs, material costs, and operational costs, leading to significant cost savings over time.
Competitive advantage: Smart manufacturing can help manufacturers stay ahead of the competition by enabling them to innovate, improve customer satisfaction, and reduce time to market.
The Role of Quality Control in Manufacturing
Quality control is an essential part of the manufacturing process. It involves the inspection of products to ensure that they meet the required standards of quality. Quality control is critical in ensuring that products are safe and reliable. Smart manufacturing can play a key role in quality control by providing real-time monitoring of production processes.
The key unresolved aspect of effective quality control in industry is the qualitative and quantitative control of chemical products that will be effective (high quality) and, at the same time, cheap and in real-time. Many systems in the world use, for example, vision inspection for the quality of mechanical components. At the same time, the chemical industry, in most cases, must carry out a complete, complicated quality control procedure, including collecting samples of chemical substances (ingredients, semi-products, products) and sending them for analysis by a specialized laboratory. Unfortunately, only a few solutions on the market could realistically ensure effective quality control directly on the production line in real-time. But most of them are too expensive to implement in most factories. That’s why at Spectrally, we are focused on solving this problem.
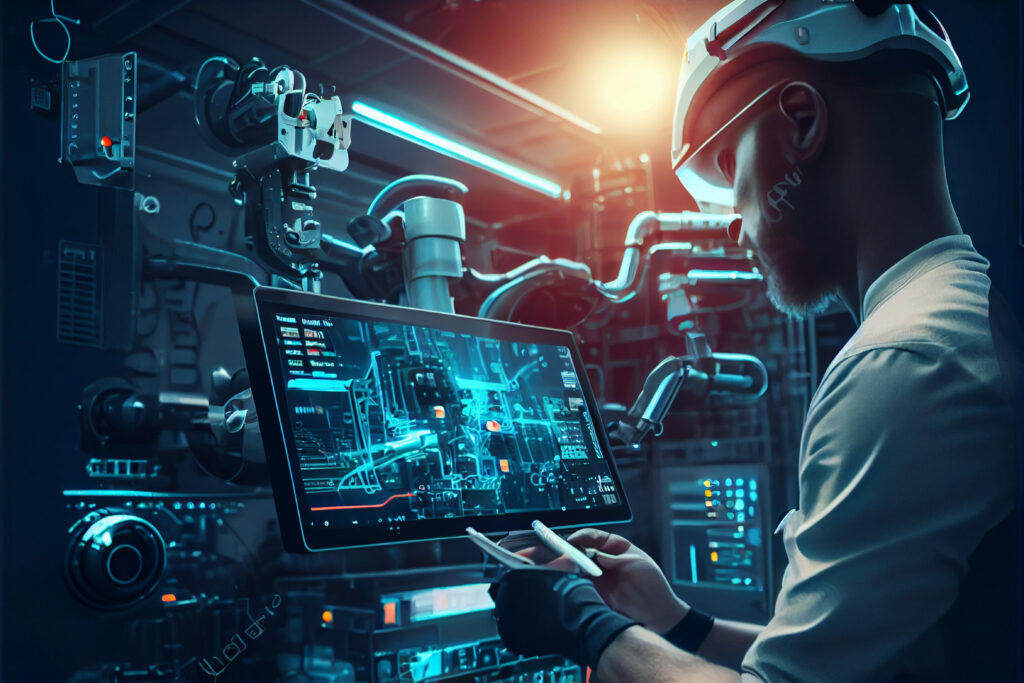
The Importance of Automated Quality Control
One way to reduce production costs and increase product profitability is to automate quality control.
Automated quality control is an essential part of smart manufacturing. It involves the use of advanced technologies, such as machine learning and artificial intelligence, to monitor production processes and identify defects in real-time. Automated quality control can help reduce the risk of human error and improve the accuracy of inspections.
Smart Manufacturing Solutions for the Cosmetics Industry
The cosmetics industry is one that can benefit greatly from smart manufacturing and real-time, automated Quality Control. The industry is highly competitive, and manufacturers are under pressure to produce high-quality products quickly and efficiently. Smart manufacturing can help manufacturers achieve these goals by optimizing production processes, reducing waste, and improving product quality.
In addition, the voluntary improvement of outdated quality control and the development of the use of new technologies will contribute not only to an increase in business profitability and reduction of production costs but, above all, to an increase in the value of products in the eyes of customers, thanks to the manufacturer’s genuine care for product quality. This is extremely important, especially for manufacturers of premium products, where the primary added value distinguishing the product on the market is its better quality.
Case Studies of Successful Smart Manufacturing Implementation
There are many examples of successful smart manufacturing implementations in chemical quality control:
- BASF – Implementation of a digital quality control system:
BASF implemented a digital quality control system to improve the accuracy and efficiency of its product testing and analysis. The system uses automated processes to analyze test results and generate reports, reducing the risk of errors and improving the speed of analysis. The system also includes a centralized database for storing and sharing test data, enhancing collaboration and knowledge management.
- Dow Chemical – Use of statistical process control:
Dow Chemical implemented a statistical process control (SPC) system to monitor and control its production processes. The system uses real-time data analysis to identify variations and anomalies in the manufacturing process and take corrective actions to prevent quality issues. The SPC system has helped Dow Chemical reduce defects, improve product consistency, and increase production efficiency.
- Merck – Adoption of a process analytical technology (PAT) system:
Merck implemented a PAT system to improve the efficiency and accuracy of its product testing and analysis. The system uses sensors and data analytics to monitor the manufacturing process and identify potential quality issues in real-time. The system also includes automated testing equipment that can perform multiple tests simultaneously, reducing the time and cost of analysis. The PAT system has helped Merck improve product quality, reduce waste, and enhance regulatory compliance.
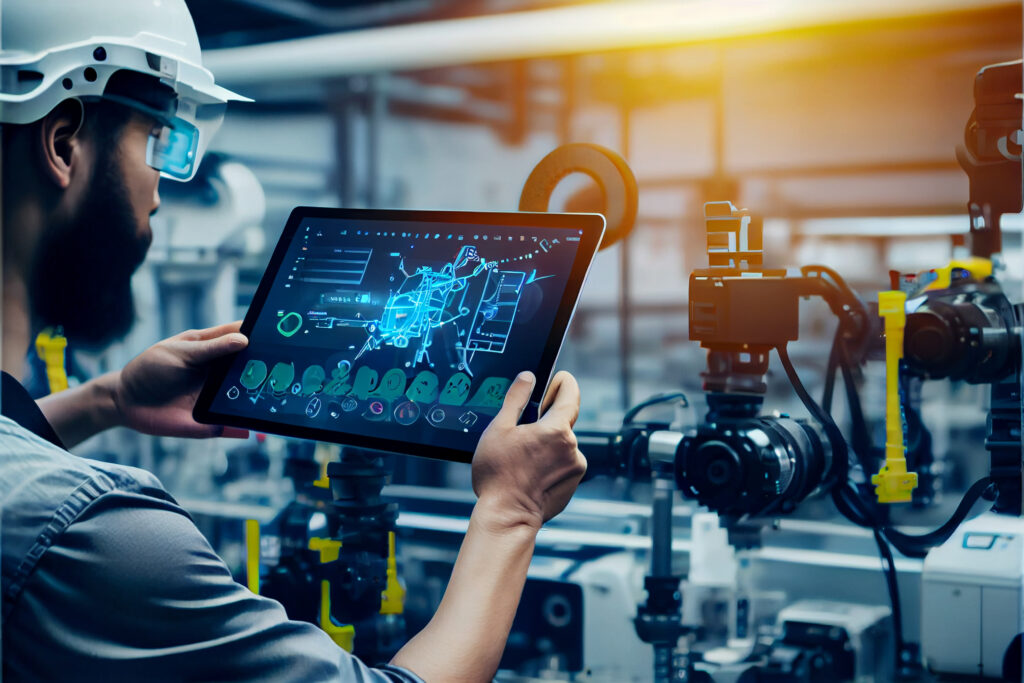
Conclusion: The Future of Smart Manufacturing in Industrial Production
Smart manufacturing is the future of industrial production. It offers numerous benefits, including increased efficiency, reduced costs, and improved product quality. By using advanced technologies, such as the Internet of Things and artificial intelligence, manufacturers can create a more efficient, productive, and flexible manufacturing environment. As the manufacturing industry continues to evolve, smart manufacturing will play an increasingly important role in driving growth and innovation.
Overall, these case studies demonstrate the benefits of innovative quality control systems in the chemical industry, including improved efficiency, accuracy, and consistency, as well as reduced costs and improved regulatory compliance.
It is, among others, care for the best quality control that contributes to the size and success of companies such as BASF, Merck, and Dow Chemical.
After improving the high-level quality control processes in production, it’s time to innovate in quality control tools. It is an ossified industry, where specialized laboratories are used in most cases, which in turn has a negative impact on the cost of the process, its duration, and potential problems with product quality resulting from too infrequent, random quality control. Providing tools for non-invasive quality measurement in real-time on the production line is another technological breakthrough happening before our eyes.
Join Smart Manufacturing revolution!
Tell us about your company’s specific requirements, and we’ll create a customized project plan that’s designed to seamlessly integrate our industry 4.0 technology into your smart manufacturing line. And the best part? We’re happy to do it all free of charge.
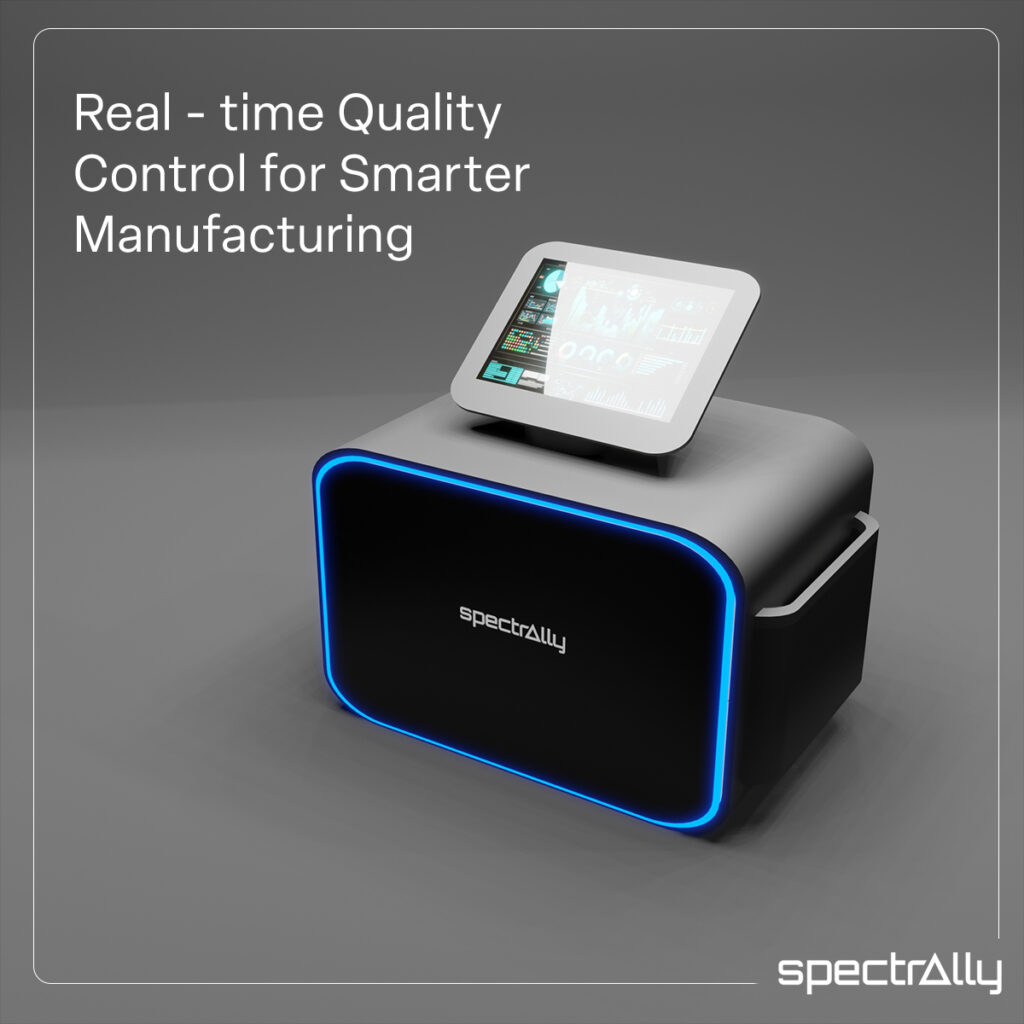